工业与机械零件的铸造与CNC加工:精密制造的双重奏
在现代工业和机械制造领域,铸造与CNC(计算机数控)加工是两种相辅相成、缺一不可的核心技术。铸造技术为复杂形状的零件提供毛坯,而CNC加工则在此基础上实现高精度、高效率的精细化成形,两者结合确保了工业与机械零件在性能、尺寸精度和表面质量上达到严苛要求。
铸造:工业零件的起点
铸造是制造工业和机械零件的基础工艺之一,它通过将熔融的金属液浇注到预先制成的铸型中,凝固后获得具有一定形状和尺寸的铸件。其主要优势在于能够生产形状复杂的零件,尤其是一些带有内部腔体或不规则外形的部件,这是其他加工方式难以比拟的。
常见的工业与机械零件铸造方法包括:
- 砂型铸造: 成本较低,适合生产大型、形状简单的铸件,如机床床身、大型箱体等。
- 精密铸造(熔模铸造/失蜡铸造): 能够生产尺寸精度高、表面光洁度好的复杂小型零件,如阀体、叶轮、液压元件等。对于航空航天、医疗器械等对精度和性能要求极高的领域尤为重要。
- 压铸: 适用于大批量生产小型薄壁、精度要求较高的有色金属合金零件,如汽车发动机部件、电子产品外壳等。
- 金属型铸造(重力铸造/低压铸造): 介于砂型铸造和压铸之间,可生产性能更好的中小型铸件。
铸造工艺赋予零件基本的几何形状和内部结构,但也存在一些固有限制,如表面粗糙度、尺寸精度相对较低,以及可能存在内部缺陷(如气孔、缩孔)等问题。这就引出了CNC加工的重要性。
CNC加工:赋予零件高精度与精细度
CNC加工是指利用计算机控制的机床对零件进行切削加工的过程。它通过预先编程的指令,精确控制刀具的运动轨迹、进给速度和切削深度,从而实现对铸件毛坯的高精度切削、钻孔、铣削、车削等操作。
CNC加工在工业与机械零件制造中的作用主要体现在:
- 实现高尺寸精度和形位公差: 铸件毛坯经过CNC加工后,能够达到微米级的尺寸精度和极高的形位公差要求,确保零件间的完美配合和装配。这对于发动机、变速箱、精密轴承等关键部件至关重要。
- 改善表面质量: CNC加工能够将铸件粗糙的表面加工成光滑、平整的工作面,提高零件的耐磨性、密封性和疲劳强度。例如,阀门密封面、轴承座孔等都需要极高的表面光洁度。
- 加工复杂特征: 对于铸造后需要进一步加工的螺纹孔、键槽、复杂的曲面或多轴联动加工的异形结构,CNC机床能轻松应对,实现自动化、高效率的加工。
- 提高生产效率与一致性: CNC加工具备高度自动化和重复性,一旦程序设定完成,即可持续稳定地生产出大批量高精度零件,大大提高了生产效率并确保产品质量的一致性。
- 弥补铸造缺陷: 通过CNC加工可以去除铸件表面的飞边、毛刺,并修复或避免一些轻微的铸造缺陷对零件性能的影响。
铸造与CNC加工的协同作用
铸造与CNC加工并非相互独立的工艺,而是紧密结合、相互依存的:
- 铸造提供近净形毛坯: 铸造技术能够将大部分金属一次成形为接近最终形状的毛坯件(即“近净形”铸造),这大大减少了CNC加工的切削余量,降低了材料消耗和加工时间。
- CNC加工提升最终品质: 铸件的尺寸精度和表面质量往往无法直接满足最终产品的要求,CNC加工正是为了弥补这一差距,将铸件提升为高精度、高性能的成品零件。
- 优化成本与效率: 对于许多复杂零件而言,如果完全通过CNC加工从实心棒材或板材切削,会造成极大的材料浪费和加工成本。而先通过铸造获得复杂外形,再通过CNC加工精修关键尺寸和表面,是兼顾成本、效率和性能的最佳方案。
典型应用实例
- 汽车工业: 发动机缸体、缸盖、变速箱壳体等通过铸造形成大致形状,再通过CNC加工完成气缸孔、阀座、安装孔和结合面等精密加工。
- 工程机械: 液压阀体、泵体、传动箱等大型复杂件,先通过砂型或精密铸造,后经大型CNC机床精加工关键尺寸。
- 航空航天: 涡轮叶片、结构支架等高性能零件,常采用精密铸造获得复杂叶型或轻量化结构,再通过五轴CNC加工实现超高精度和表面完整性。
- 通用机械: 各类齿轮箱、泵阀、电机壳体、工装夹具等,都离不开铸造与CNC加工的协同配合。
总而言之,铸造提供了工业与机械零件的宏观成形能力和材料性能基础,而CNC加工则赋予这些零件无可挑剔的尺寸精度、表面质量和功能性。两者相互补充,共同构成了现代工业精密制造的核心支柱,推动着各行各业的技术进步和产品升级。
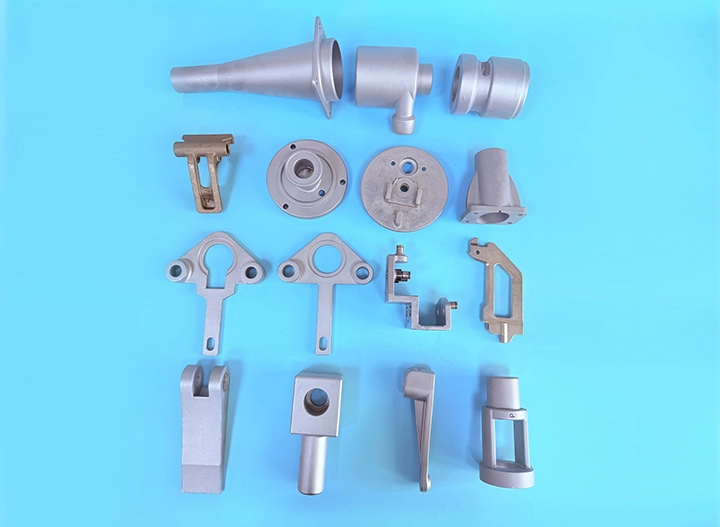
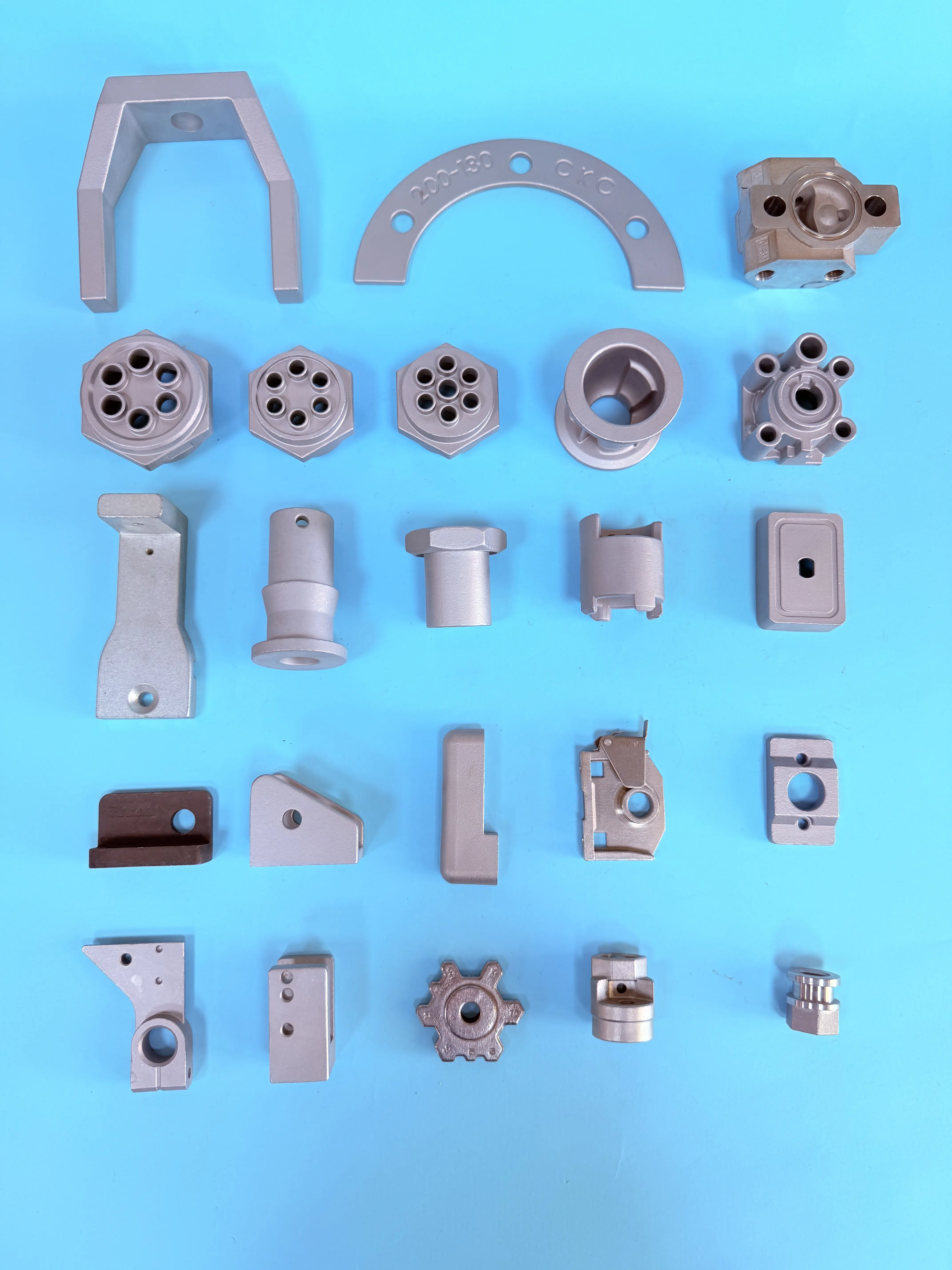
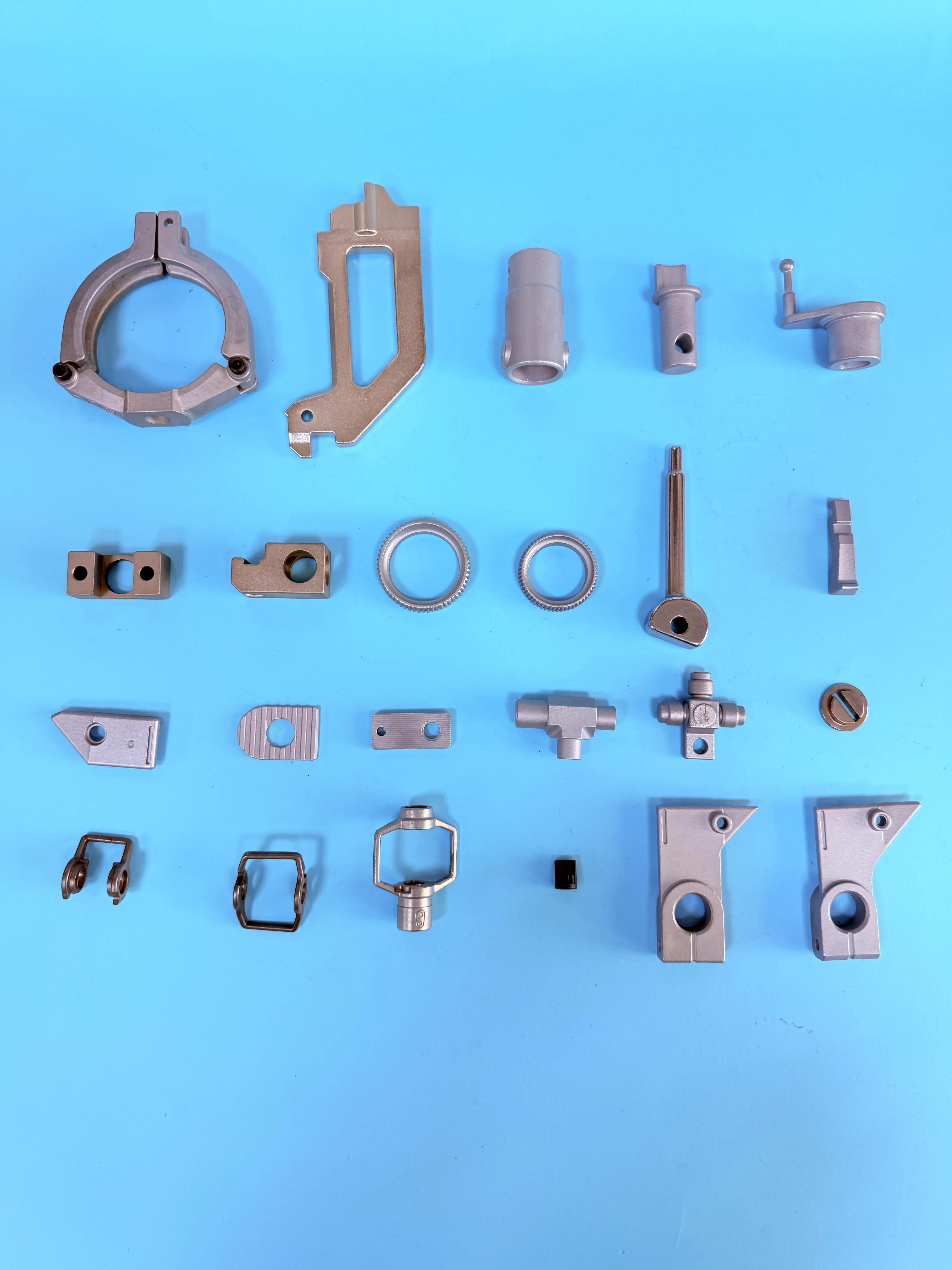
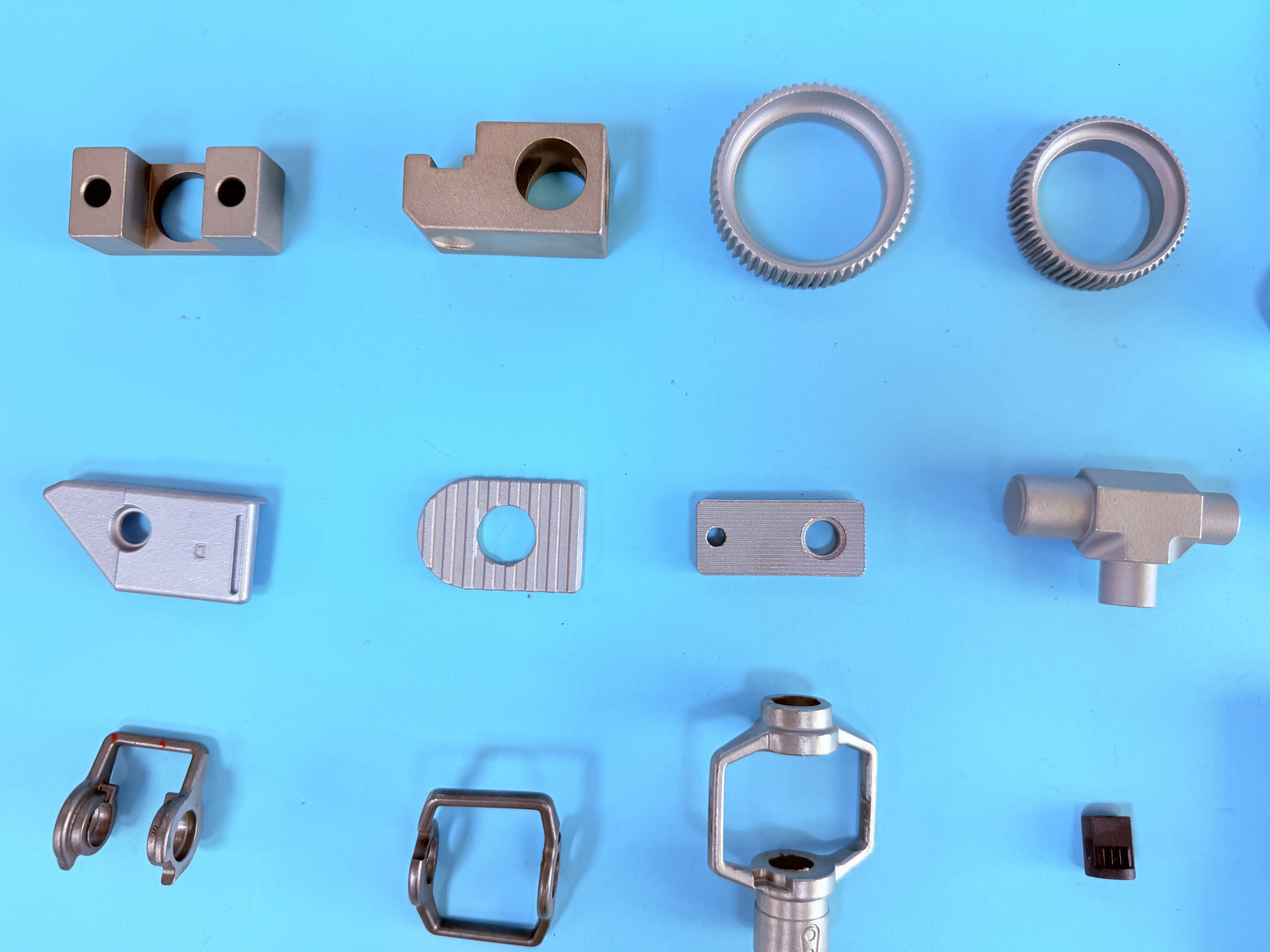
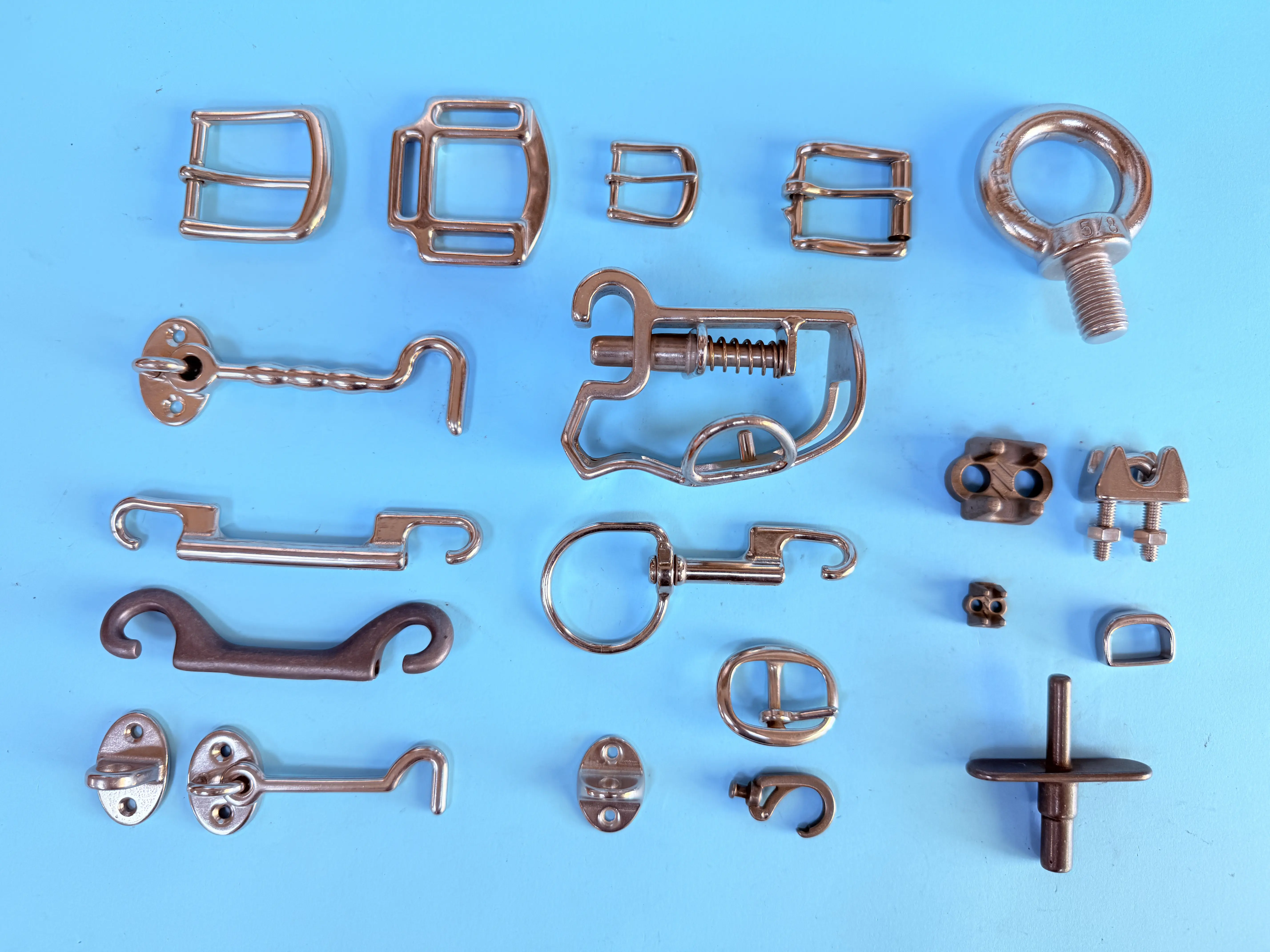